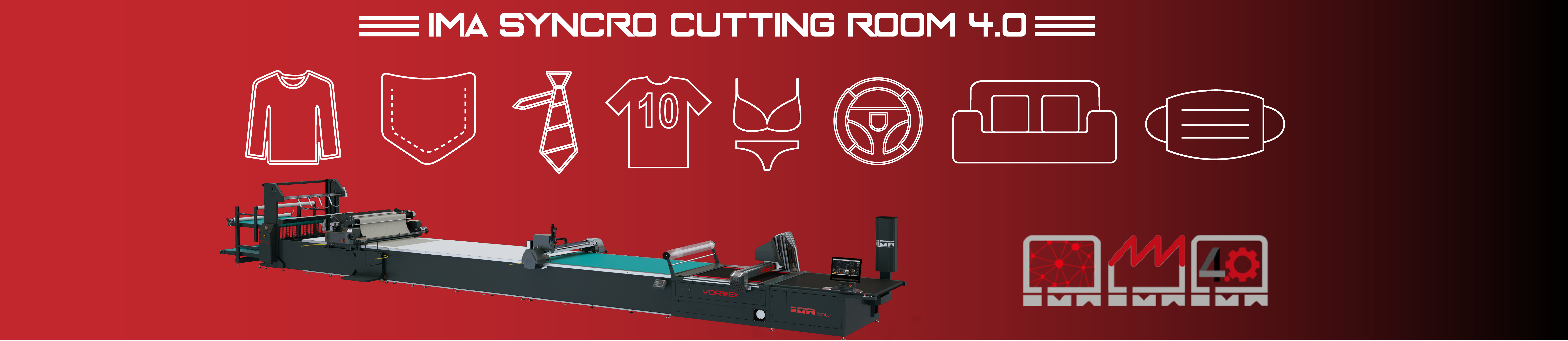
IMA is Industry 4.0 as it meets the concept of automated and interconnected production.
IMA technology translates into the optimization of consumption and performance, saving energy resources and more, looking to the future with a view to sustainability.
The change is already here: be part of it!
Thanks to digital technology, IMA machines are able to collect and manage the data, as well as to return and interchange them with external systems. This is why they can benefit from incentives for business innovation.
IMA has been on this path since long time, when in 2013 it introduced the first line of products totally based on digital technology, taking a big step forward in the direction of Industry 4.0.
State-of-the-art solutions that allow you to connect next-generation management and control systems with customer management systems so that to plan production, monitor it, analyze data in real time and identify areas of intervention to improve productivity.
All this to optimize the management of the plants and enter a new era of the fully automated and “lean oriented” factory.
The latter concept is still not very understood, a philosophy of thought and a concrete action that involve the improvement of the internal conditions of the business processes to obtain an excellent output.
Lean Production and more generally Lean Thinking is increasingly seen as a way of thinking and a philosophy to follow as it refers to everything that is necessary to improve flexibility, quality and the entire company production structure, starting from 5 fundamental principles:
• identification of the value perceived by the Customer
• identification of the activities that create value perceived by the customer,
resulting in the elimination of waste
• creation of a smooth flow of activities that create value
• synchronization with the requests of the customer and therefore of the market
• pursuit of perfection, through continuous improvement.
Remove what is not needed, preserve what is necessary, implement what the company needs, always having as a reference the value perceived by the Customer.
Analysis of production systems, intelligent factory design according to the different needs, implementation of software and integration systems, supply of machinery, final installation and constant monitoring are the goal for our customers.
All this translates into a perfect integration of the systems and automation of production processes that will definitely change the idea of production and productivity.